SimpiFlow™ by PF Tech
The SimpliFlow™ is the revolutionary powder hopper engineered to ensure precise and stable powder delivery to your process.
It is designed for Thermal Spray, Laser Cladding, PTA and Powder Additive processes.
VISIT PF TECH WEBSITE
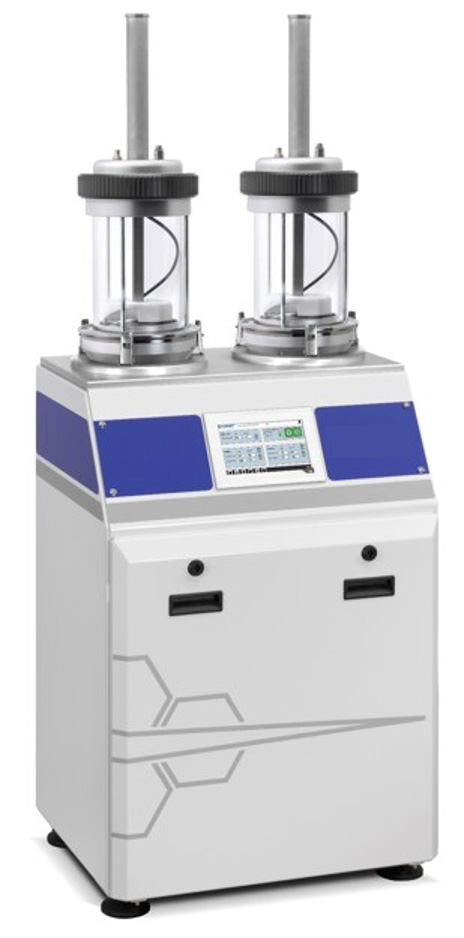
- Precise stable feeding at low to high feed rates, pulsation free
- Accepts very wide powder particle size range, very fine to coarse and blends.
- Easily feeds freely-flowing and non-freely flowing powders
- 3.0L canister for extended production runs
- Fits to your existing standard volumetric rotary powder feeder
- Only one wear part
- Strip and clean in only a few minutes,
- The pick-up disc is quickly replaceable
- Rated to 7 bar
- Powder is taken from the top rather than the bottom, eliminating powder compaction
- Foreign particles in the powder do not influence feed stability
- Suitable for thermal spray, laser cladding processes and power-fed additive manufacturing process
- The inner glass jar acts as powder storage container, supplied with lid and evacuation valve
- Allows for safe powder handling
- Cleaning and filling of the inner glass canister can be achieved remotely in a vented room or box